The project – the latest to work with start-up New Frontier Technologies – takes advantage of tech that can scale the production of large-scale carbon composite structures which can handle the extreme loads, vibrations and shocks of blast-off.
The $180-million iLAuNCH trailblazer is a partnership between academic institutions and more than 20 industry partners aimed at accelerating the development of the space manufacturing sector.
“This is another world-class approach to lay up space-grade carbon-fibre and then digitally model that for scale and repeatable design,” said iLAuNCH Trailblazer executive director, Darin Lovett.
“As we make progress in developing sovereign capability for space applications, we know these products will also benefit defence, aerospace, and other sectors that require high-value, bespoke composite structures.”
The latest collaboration will also work with ANU and the National Laboratory for X-ray Micro Computed Tomography (CTLab) for testing.
Using an ANU high-resolution CT scanner to assess and mature the manufacturing process, the project will build a “digital twin” of the rocket bodies to assess and improve the fidelity of structural models for simulation.
“The application of X-ray computed tomography (CT) and 3D multiscale modelling at ANU will provide high-fidelity simulation,” said iLAuNCH.
“The CT will capture the detailed microstructure features, such as fibre alignment and voids, that can be reflected in the simulation models.
“3D models will provide a detailed digital profile, with capability for performance simulation of every manufactured component, which is the foundation for digital certification.
“The project lead, New Frontier Technologies, has developed innovative design-for-manufacture (DfM) strategies for scalable, additive manufacturing of space-grade carbon-fibre structures using laser-assisted automated tape placement (ATP).”
It comes after Space Connect reported in October how iLAuNCH would work with New Frontier Technologies to develop light, radiation-proof coatings for LEO satellites.
The organisation said it hoped the project would ultimately bring down the cost of launch, given payloads are usually billed per kilogram of weight by launch providers.
The coatings have to balance saving weight with being able to withstand a range of environmental hazards experienced in LEO, such as UV irradiation, atomic oxygen and space debris.
“These environmental hazards can cause surface erosion, cracking, and delamination of composite materials, which can lead to a reduction in the mechanical properties of the material and can compromise the structural integrity of the spacecraft,” said iLAuNCH.
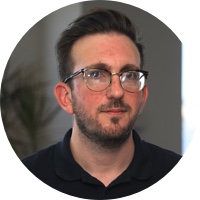
Adam Thorn
Adam is a journalist who has worked for more than 40 prestigious media brands in the UK and Australia. Since 2005, his varied career has included stints as a reporter, copy editor, feature writer and editor for publications as diverse as Fleet Street newspaper The Sunday Times, fashion bible Jones, media and marketing website Mumbrella as well as lifestyle magazines such as GQ, Woman’s Weekly, Men’s Health and Loaded. He joined Momentum Media in early 2020 and currently writes for Australian Aviation and World of Aviation.